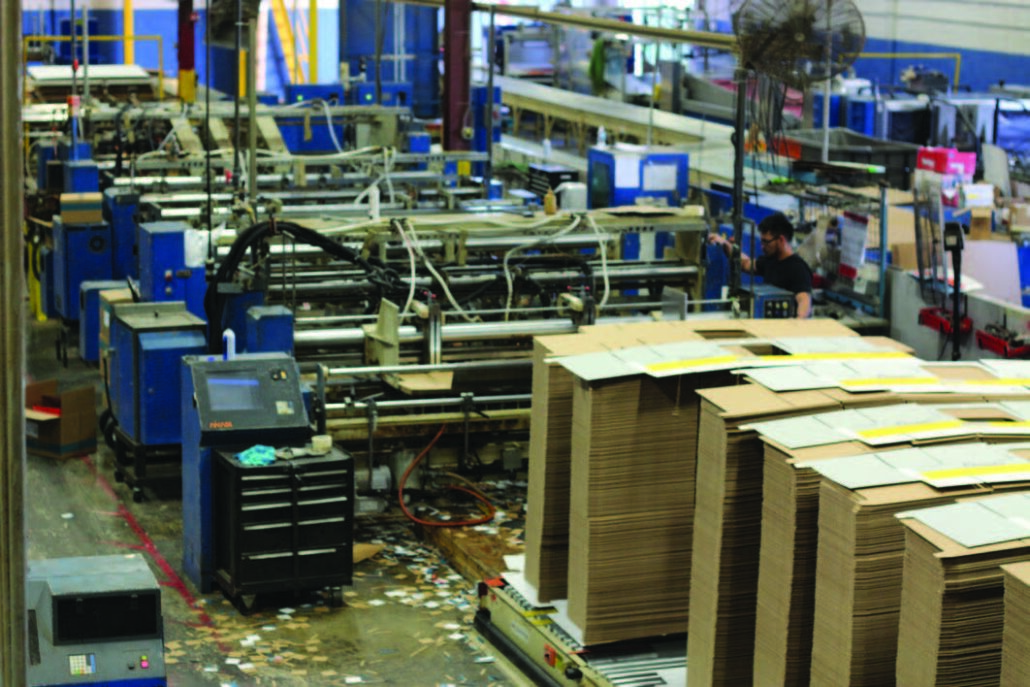
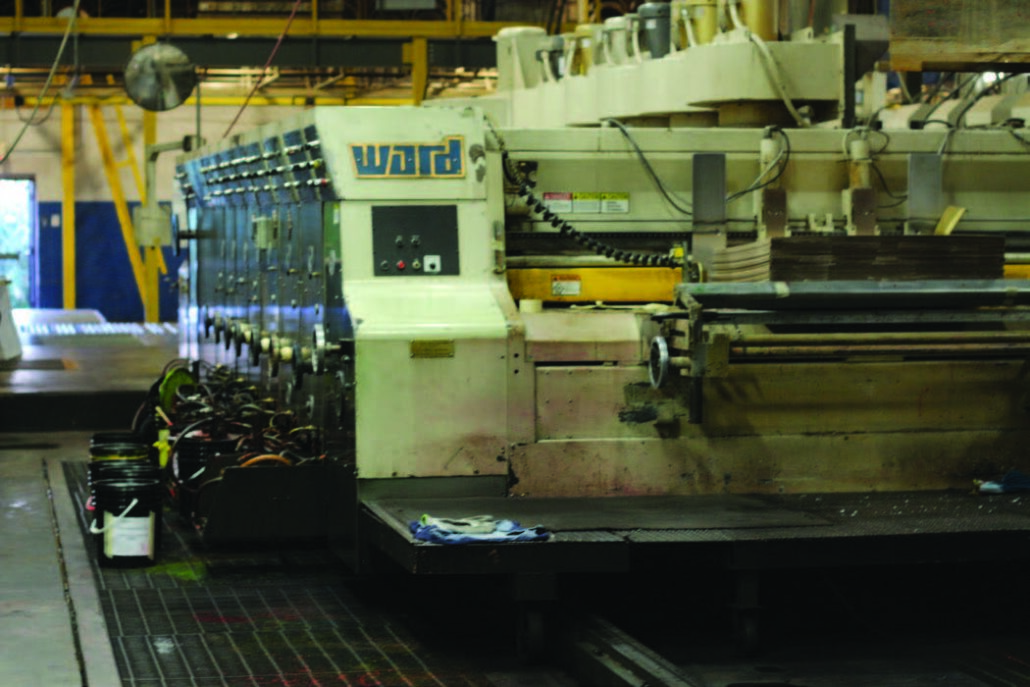
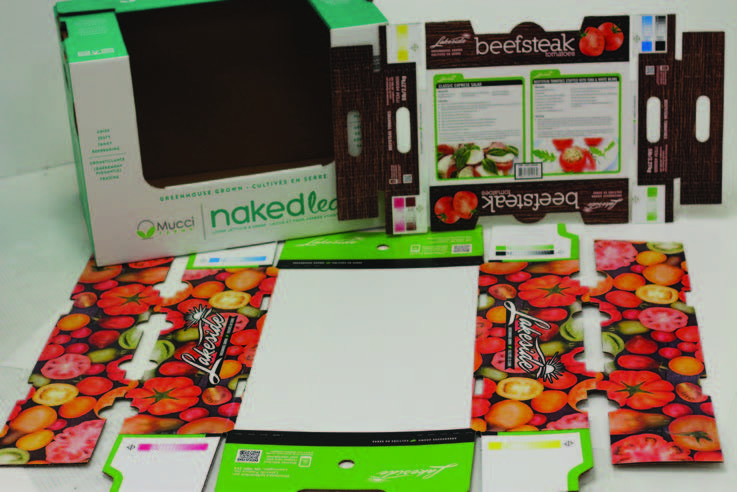
SunTrac Vacuum Transfer upgrade improves performance of 1986 Martin RapidSet
Mid-Atlantic Packaging Inc. (MAP) was established in 1961 as a privately held and veteran owned company. Since its inception, MAP has been a leader amongst corrugated box manufacturers, and its mission has been to deliver corrugated packaging products and services to customers that meet and/or exceed their expectations. From its Montgomeryville, PA facility, MAP works a two shift operational with 165 employees. The company does everything from corrugating its own board to printing, die-cutting and gluing. What sets the company apart from its independent counterparts is horsepower. Around the early 1990’s the company began investing heavily in providing more value-added solutions and ultimately more horsepower to meet demands. Today MAP answers the call with three, 7-color rotary die cutters and three specialty gluers.
“We are still very much involved in brown box, but we are far more recognized for our specialty work,” says, Joseph Hodges, Operations Manager at Mid-Atlantic Packaging, Inc. “As such, there are higher standards for production and print quality so keeping our equipment in optimal condition is a top priority. And while we rely on our 20+ year veteran employees for most machine maintenance and fixes, we rely on our vendors to supply right solutions for our growing challenges.”
We can go to SUN and say: ‘this is our problem, what can you do,’ and trust the response to be genuine and in our best interest.
One recent challenge involved the company’s 1986 Martin with RapidSet. The machine had been preforming well for decades. It wasn’t until several years ago that it started having issues with registration and reliability of the pull collars.
“The machine needed to be fixed or replaced,” says Larry Norelli, Maintenance Manager at Mid-Atlantic Packaging. “It would be very expensive to replace the entire unit and we don’t have the space to even put the same model machine back in because of the building columns and new guarding on the machine.”
Needing a creative resolution, MAP turned to long-time partner SUN Automation Group® (SUN). As a leading provider of innovative solutions for the corrugated industry, MAP trusted SUN to rise to the challenge.
“We like the fact we can go to SUN and say: ‘this is our problem, what can you do,’ and trust the response to be genuine and in our best interest.” Says Hodges. “It’s an added bonus that they are a US manufacturer with ample parts and service.”
So when time came to look at the Martin, SUN knew immediately what needed to be done and suggested its SunTrac® Vacuum Transfer system. The simple retrofit is available for both top and bottom printing equipment and works by keeping boards in a firm position throughout the machine. By enabling optimum board path from print nip to print nip, SunTrac further eliminates jams and improves speeds and print quality. It also allows MAP to run small flute board effortlessly to meet growing market demand and removes many of the high maintenance items that also make up for long set-up times.
But before MAP could reap the benefits of this retrofit, it needed to be installed. Looking to minimize downtime, SUN worked with MAP to ensure the process wouldn’t disturb operations and increase customer lead times. To accomplish this, the four-color machine was broken into sections, with a two-color section removed and placed in the back of the plant. After a one week tear down, where obsolete components are removed and new SUN technology is installed, the section was ready to be put back in. The following week it was installed along with the vacuum transfer and the next section was pulled out and improved as well.
“When we did each of the sections and put in the new retrofit, the machine went off and running,” says Norelli. “We lost very little time for the whole retrofit and saw immediate results.”
In fact, speeds nearly doubled and quality improved immediately leading to more than a 25% increase in production on every run. Precise control of sheet travel from frame to frame also meant that lead and tail trip could be reduced or eliminated. But the savings did not end there. SunTrac installation enables the removal of the pull collars and shafting– freeing up space and reducing future maintenance costs as most of the parts previously needing more maintenance have been permanently removed. In addition, workers have more room to work on the machine and simpler controls and electrical components to operate it. The additional space can also be used to create a dwell space between the last print unit and the die-cut unit to avoid print distortion caused by the die-cutting process. It can also be used to install dryers.
“All in all, it’s a great retrofit and SUN is a great outfit” says Norelli. “Our operators and supervisors are also pleased by the fact it’s simplified operations while simultaneously increasing productivity.”
“I think, for us, what sets SUN apart is not just any one dimension. As we mentioned already, we love having a relationship with somebody that is close by but ultimately, we have great confidence in their service, offerings, products and people that we work with. So whether it be for print transfer needs or general machine maintenance and upgrades, we have no hesitations turning to SUN to help us with our needs.”