There are multiple quality Flexo Folder Gluer (FFG) manufacturers in the market, but not every machine offers the features you need to produce the boxes in your current or aspiring order mix, efficiently and economically. Auditing your print jobs and process aspirations is the key to understanding what machine features you’ll need to achieve your goals, for long runs or small orders. There are many things to consider when purchasing a Flexo Folder Gluer, and if your due diligence is not thorough, you could be making the wrong decision for your company. Consider the following when deciding on the right capital investment for your order mix, your employees and your future.
Long Run Print Jobs (> 5,000)
Flexo Folder Gluers have evolved into fast, powerful workhorses, capable of high speed converting of sheets, to meet the demand of the corrugated packaging industry. If primarily converting corrugated board in mass quantities, consider the following in your purchase of an FFG.
Open/Close Systems
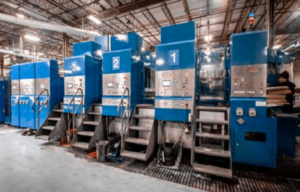
If you are seeking a Flexo Folder Gluer to increase capacity and productivity and have few changeovers per shift, an Open/Close system may make the most sense for your operations. Open/Close systems do not allow operator access to the internal machine components during production. The configuration is either off and open for job changeovers or closed for production – there is no in between. These powerful FFG systems, like the Latitude P-Series, are built for speed and capacity, getting those large orders out the door efficiently and effectively.
In our experience serving box makers, we believe that an Open/Close FFG is best for printers producing 10 or less print jobs per shift. We’ve observed printers spending between 20-30 minutes preparing an Open/Close machine between jobs, and that downtime can add up if job changes become frequent. For example, let’s say the machine can produce an ROI of $1,000 per hour, and it takes operators 30 minutes for changeovers; with 10 job changes per shift, you would have about 5 hours of machine downtime, losing virtually $5,000 per shift. This could add up to a whopping 5+ million in loss value every year, assuming 24/7 operations. That’s why speed, capacity and quality are the highlight of these converting workhorses, making them a smart option for converters with few job changes per shift.
Set While Run
Although Open/Close systems have been the system of choice for mass box production, some corrugated converters are finding that Set While Run machines can optimize their work force during long run orders. We have witnessed Converters reduce the number of operators per shift, using Set While Run technology, while still maintaining their machine productivity and box quality. During long runs on an Open/Close machine configuration, operators may have down time as they wait for orders to complete before setting the machine for the next job. However, with Set While Run, one press operator can float between multiple stations and prepare other machines for the next order in the queue. Printers taking advantage of this method can maximize their operators’ time on the floor and reduce downtime immensely.
Short Run Print Jobs (< 5,000)
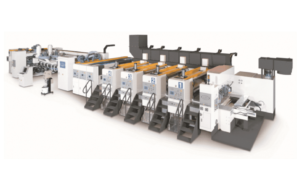
As order mixes shift from millions of shipping boxes to seasonal branding vehicles, short runs have quickly become the money makers of the box industry… if you have the equipment to produce them efficiently. Orders of 5,000, or less, are now more common than ever and a Set While Run machine is the choice for this order mix. Here’s why…
Set While Run
For Corrugated Printers producing 10+ print jobs consistently per shift, we recommend Flexo Folder Gluers that are Set While Run. Set While Run technology allows operators to prepare unused print stations for the next job order, while the machine is still producing the first. Access to the plate cylinders, ink stations and other components are available while the machine is still in production. This allows operators to change plates, modify inks and prepare other consumables for the next job, without interrupting production. When a short run is done, the operator need only to perform a few simple tasks to begin the next order. With minimal downtime, ease of operations and high-quality printing and folding, Set While Run FFGs, like the Latitude PP-Series with inside printing capabilities, are a solid choice for dynamic printers producing small quantities throughout the days.
Long & Short Run Mix
But what if your order mix changes by season? What if it’s practically half and half? If throughout the year there is seasons of both long runs and short runs, a Set While Run machine is the best option for your operations. During seasons of small order quantities, the ability to set the machine for the next order, during production, is a must in order to remain competitive. When the long run contracts renew, having a machine that is powerful and fast is key to remaining productive and profitable. LMC’s unique/smart design make the set while run machine a very affordable option over the open close configuration without increasing the required machine footprint. The flexibility and functionality offered by a Set While Run configuration makes it a great hybrid option for converters who navigate seasons of large and small order quantities.
Custom FFG Generator
Purchasing a new Flexo Folder Gluer is a risky venture that converters take with the hope of solidifying their future within the box industry. SUN Automation is happy to assist you in your search for the perfect Flexo Folder Gluer for your order mix and your future. Take advantage of the SUN Custom FFG Generator – send us your order mix and production goals, and our system can calculate which Flexo Folder Gluer size, configuration, color stations and machine features would generate the best ROI for your operations. For decades, SUN has provided quality corrugated converting equipment to the box industry with the parts and service support you know and trust. With the partnership between SUN Automation and Latitude Machinery, SUN Automation now offers quality Flexo Folder Gluers and other Latitude equipment to the North and Central American markets. Latitude Machinery Corp. manufactures Flexo Folder Gluers ranging from Mini to JUMBO, and are “probably the best machine as far as boxes of any plant we have in our company” according to Brian Fitch, General Manager of Premier Packaging, Indianapolis facility. LMC is a Taiwanese company located in the independent nation of Taiwan and a long-time ally of the United States. Speak with a Specialist to discuss your capital equipment goals and how we can assist you with Everything Corrugated Under SUN.